Understanding **Plastic Molding Manufacturing**: A Deep Dive
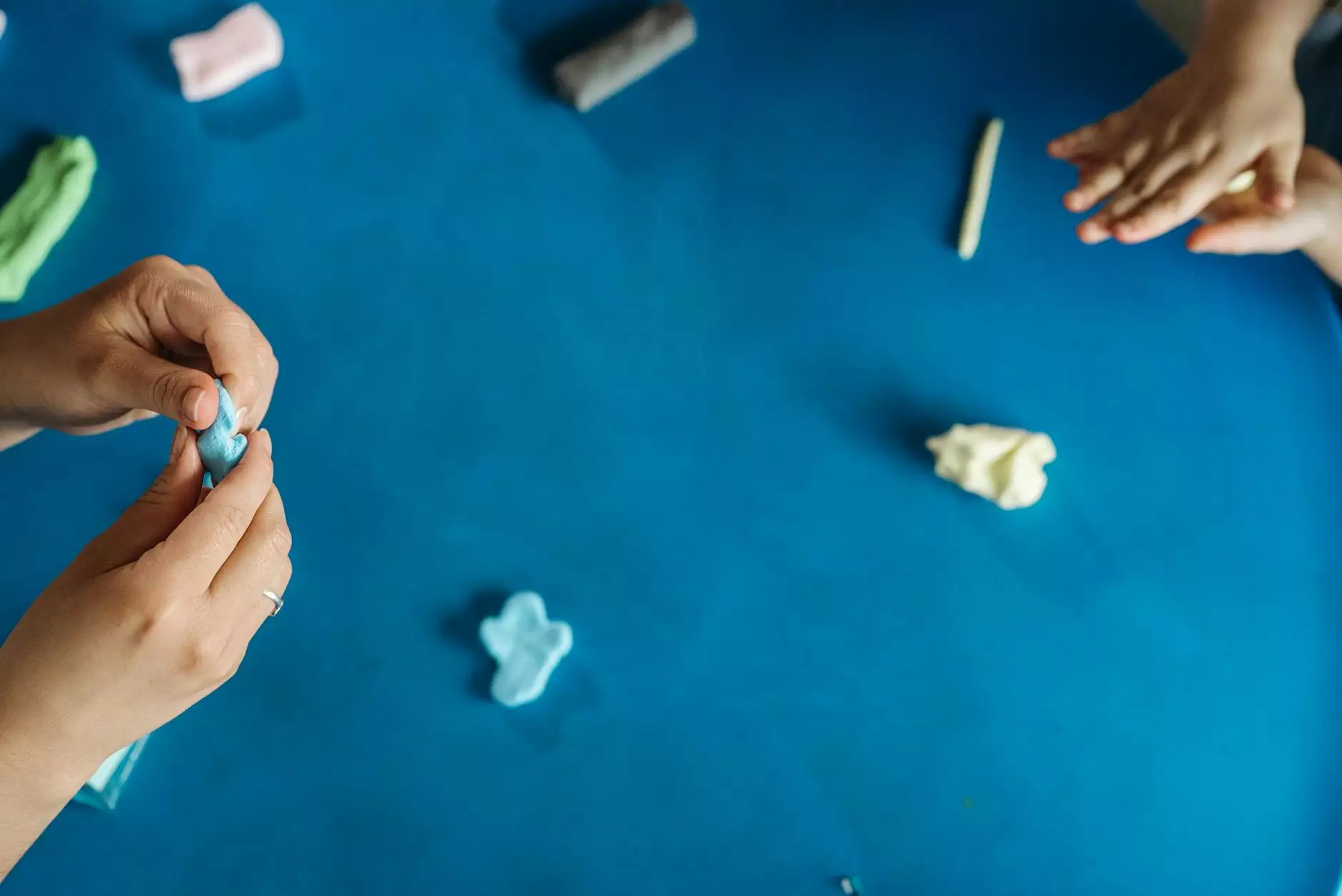
Plastic molding manufacturing is a critical component of the modern industrial landscape. This article aims to provide a thorough exploration of the principles, processes, and benefits of plastic molding as a manufacturing method. We will delve into its applications across various sectors, emphasizing its significance in metal fabrication and other related industries.
The Basics of Plastic Molding Manufacturing
At its core, plastic molding manufacturing involves the transformation of raw plastic materials into a final product through a series of processes. The fundamental principle is to heat the plastic until it becomes malleable, then shape it within a mold before allowing it to cool and solidify.
Types of Plastic Molding Processes
There are several types of plastic molding processes, each suited for specific applications:
- Injection Molding: The most common method where plastic pellets are melted and injected into a mold to create a specific shape.
- Blow Molding: Used primarily for hollow objects, this process involves inflating hot plastic into a mold.
- Compression Molding: A pre-measured amount of plastic is placed in a heated mold and compressed to shape, typically used for thermosetting plastics.
- Rotational Molding: Involves heating plastic in a mold that rotates, evenly coating the interior surface, ideal for large or hollow parts.
- Thermoforming: Heating a plastic sheet and forming it into a mold using vacuum or pressure.
Applications of Plastic Molding Manufacturing in Modern Industry
Plastic molding is incredibly versatile, with applications spanning various industries. Here are some significant areas where plastic molding manufacturing plays a pivotal role:
1. Automotive Industry
The automotive industry relies heavily on plastic molded components for everything from dashboard panels to intricate engine parts. These components are lightweight, reduce fuel consumption, and lower emissions—making them indispensable in modern vehicle design.
2. Consumer Electronics
In consumer electronics, the need for durable yet lightweight cases for devices such as smartphones and laptops drives the demand for plastic molding. Precision molding ensures a perfect fit for intricate internal components, enhancing the overall quality of the final product.
3. Medical Devices
Medical devices often require high precision and sterilization capabilities, which plastic molding can accommodate. From surgical instruments to housings for complex machinery, plastic molding provides the necessary flexibility and reliability.
4. Packaging Solutions
The packaging industry benefits from plastic molding through the production of containers, bottles, and custom packaging solutions. It allows for the efficient production of lightweight materials, reducing shipping costs and improving sustainability.
5. Construction Materials
In building and construction, molded plastic components are used to create fixtures, fittings, and even structural elements. Their resistance to moisture and corrosion makes them ideal for various environments.
Advantages of Plastic Molding Manufacturing
The advantages of incorporating plastic molding into production processes are extensive:
- Cost-Effectiveness: High-volume production leads to reduced per-unit costs, making it ideal for mass production.
- Design Flexibility: Complex shapes can be achieved easily, allowing for innovative designs and custom applications.
- Material Efficiency: Minimal waste is produced during the manufacturing process, contributing to a more sustainable operation.
- Speed of Production: The setup time and cycle times in molding processes are typically shorter than other manufacturing methods.
- Durability: Molded plastics often demonstrate superior resistance to various environmental impacts, including temperature fluctuations and chemicals.
Environmental Considerations in Plastic Molding Manufacturing
As industries strive for sustainability, plastic molding manufacturing has evolved to incorporate eco-friendly practices. The use of recycled materials in plastic molding processes reduces reliance on virgin plastics and promotes circular economy principles.
Recycled Plastics in Molding
Utilizing recycled plastics not only diminishes environmental impact but also supports industry growth. Manufacturers are increasingly investing in technologies that facilitate the recycling of post-consumer waste into high-quality molding processes.
Energy Efficiency
Modern advancements in machine technology are leading to significant improvements in energy efficiency within plastic molding operations, further contributing to their sustainability credentials.
Future Trends in Plastic Molding Manufacturing
The future of plastic molding manufacturing is poised to be shaped by several key trends:
1. Automation and Smart Manufacturing
The rise of Industry 4.0 has introduced automation into molding processes, optimizing production lines and reducing human error. Smart technologies enhance monitoring, maintenance, and operational efficiency.
2. Advanced Materials
Developments in materials science are leading to new types of plastics that provide enhanced performance characteristics. These may include bio-based plastics and composites that offer greater strength and resistance.
3. Customization and On-Demand Production
With advancements in 3D printing and rapid prototyping, manufacturers are now able to offer customization options that were not feasible previously. This trend allows for more personalized products that cater to specific consumer needs.
4. Focus on Sustainability
The environmental responsibility movement will continue to grow, driving demand for sustainable production practices, including the use of biodegradable plastics and energy-efficient manufacturing processes.
Choosing the Right Plastic Molding Manufacturing Partner
When it comes to choosing a plastic molding manufacturing partner, keep the following factors in mind:
- Experience and Expertise: Look for manufacturers with a proven track record and industry knowledge.
- Technological Capabilities: Assess the technology and machinery they employ to ensure they can meet your production needs.
- Quality Assurance: Ensure they have robust quality control processes to deliver reliable products.
- Environmental Policies: Partner with companies committed to sustainable practices.
- Customer Support: Good communication and customer service will help facilitate a successful working relationship.
Conclusion: The Impact of Plastic Molding Manufacturing on Industries
In conclusion, plastic molding manufacturing is an essential cornerstone in the production processes of countless industries. Its versatility, cost-effectiveness, and ability to facilitate innovation make it an invaluable resource in the current market landscape. As technology advances and the focus on sustainability intensifies, plastic molding is set to play an even more significant role in shaping the world of manufacturing. By understanding its intricacies and potential, businesses can harness the power of plastic molding to drive their success in the years to come.