The Power of China Mould Manufacture in Modern Industry
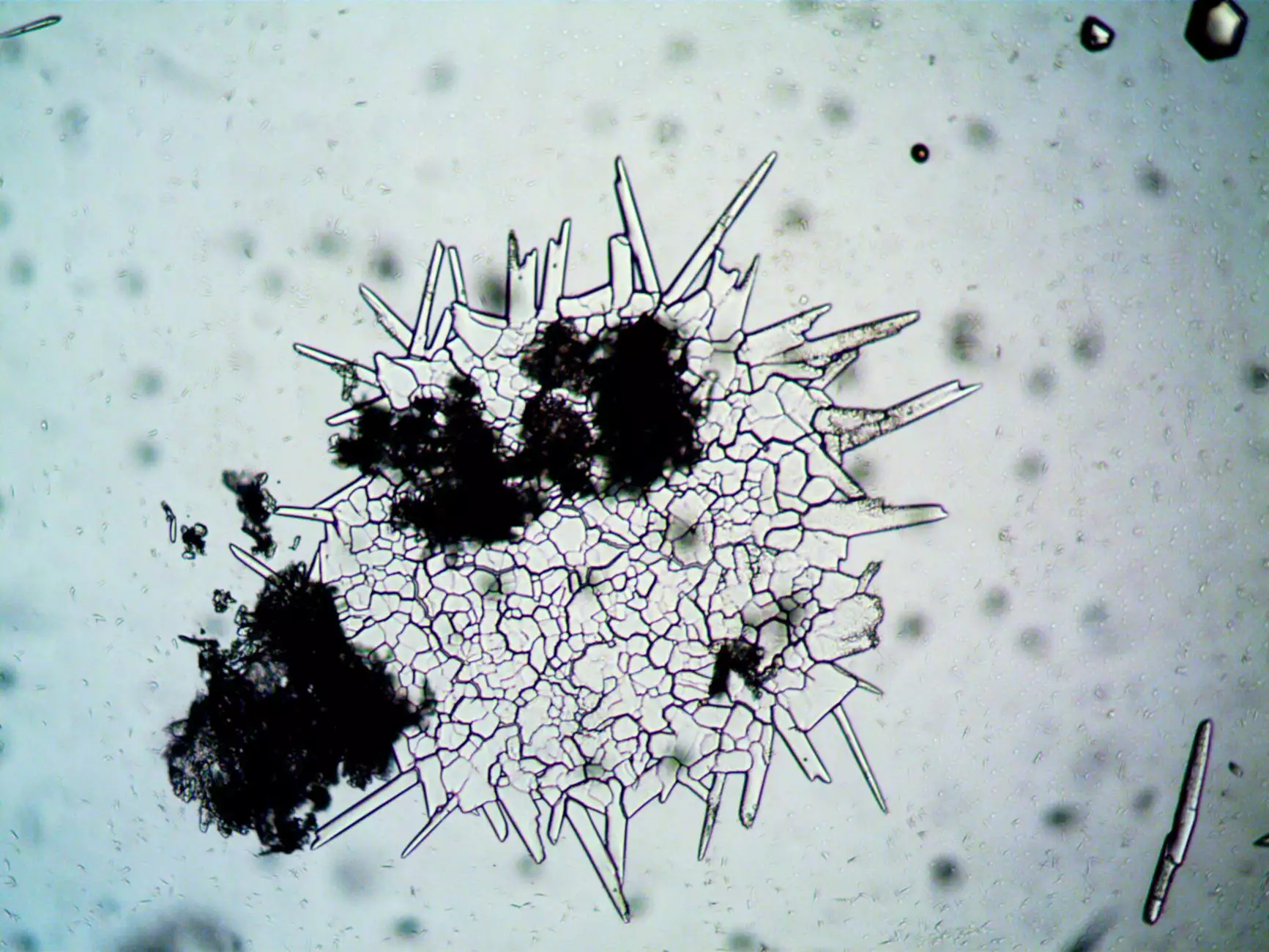
In today's rapidly evolving industrial landscape, the importance of china mould manufacture cannot be overstated. As businesses globally seek cost-effective solutions that do not compromise quality, China has emerged as a powerhouse in the mould manufacturing sector. This article delves deep into the realms of plastic mold making and plastic injection mould manufacturing, highlighting the strengths and advantages offered by Chinese manufacturers such as hanking-mould.com.
Understanding China Mould Manufacture
The term china mould manufacture refers primarily to the production of molds used across various industries, primarily plastics, automotive, consumer goods, and electronics. Molds are essential tools for shaping materials into defined forms, and the quality of these molds directly impacts the efficiency and effectiveness of production processes. The Chinese mould manufacturing sector has developed into a global leader, focusing on technological advancements and productivity enhancements.
Advantages of Sourcing Moulds from China
- Cost Efficiency: One of the primary reasons businesses turn to Chinese manufacturers is the ability to produce high-quality molds at a reduced cost. With lower labor costs and bulk production capabilities, Chinese manufacturers pass these savings onto their clients.
- Advanced Technology: Chinese mould manufacturers have adopted advanced technologies and machinery that ensure high precision and quality in production. This technological investment means that companies can expect superior products that meet international standards.
- Customization: Companies like Hanking Mould offer tailored solutions to meet specific requirements, whether for unique designs or specific production conditions. This level of customization is essential for industries with varying needs.
- Rapid Production Times: Advanced manufacturing processes allow for shorter lead times, meaning that businesses can get their products to market quicker, a crucial factor in today’s fast-paced business environment.
- Experienced Professionals: Many Chinese manufacturers employ highly skilled engineers and technicians who understand the complexities of mould design and manufacturing. Their expertise ensures that clients receive high-quality products that perform reliably.
The Plastic Mold Making Process
Plastic mold making is a specialized skill that involves creating a mold to produce plastic parts. The process includes several key stages:
1. Design and Engineering
The first stage involves thorough design considerations. Skilled engineers create a digital model using CAD software, which ensures precision and feasibility. Key factors such as cooling channels, ejector pins, and draft angles are meticulously calculated to optimize the mold's efficiency.
2. Material Selection
The choice of materials is crucial in china mould manufacture. Different plastics have varying properties, and manufacturers select materials that best suit the intended end-product functions. Common materials include steel and aluminum, each chosen based on durability and cost-effectiveness.
3. Machining and Fabrication
Once the design is approved, the fabrication phase begins. Advanced CNC machines and EDM (Electrical Discharge Machining) are used to achieve precise mould components. This stage determines the mold's structural integrity and overall quality.
4. Assembly and Testing
After machining, all components are assembled. Post-assembly, the mould undergoes rigorous testing to ensure it meets quality standards. This step verifies that the mold can withstand the production process while delivering accurate results.
5. Production and Quality Control
Finally, the mold is used in production. Quality control processes are inherent throughout the production cycle, where samples are tested to ensure they meet predefined criteria before mass output. Continuous quality assurance maintains high standards throughout.
Plastic Injection Mould Manufacturing Overview
Plastic injection mould manufacturing involves inserting molten plastic into a predefined mold, allowing it to cool and solidify into a finished part. This method is widespread due to its efficiency and ability to produce complex shapes. Let's explore how this process works:
1. Injection Process
During the injection process, plastic granules are heated until they become liquid, then injected into the mold under high pressure. The precision of this step is critical—molds must be expertly designed to avoid issues like flash or incomplete filling, which can compromise product quality.
2. Cooling Cycle
Once injected, the plastic must cool and harden, forming the final product. The cooling cycle is critical and can significantly affect production speed and efficiency. Manufacturers optimize this stage by designing cooling channels within the mould.
3. Ejection
After cooling, the mould opens to eject the newly formed part, which can then be cleaned and finished if necessary. The timing of the ejection process is vital to prevent defects.
4. Finishing and Additional Processes
Depending on the product requirements, additional processes such as painting, assembly, or quality inspections may be undertaken to ensure the end product meets all specifications.
Quality Assurance in China Mould Manufacture
Quality assurance is paramount in the mould manufacturing process. Chinese manufacturers follow several protocols to ensure that each mold produced meets industry standards:
- ISO Certification: Many leading Chinese manufacturers are ISO certified, demonstrating their commitment to maintaining high-quality production and management practices.
- Regular Inspections: Throughout production, regular inspections ensure that every component is manufactured to specification, identifying any potential issues early in the process.
- Client Collaboration: Close collaboration with clients ensures that feedback is integrated into the design and production stages, refining the final product to meet specific needs.
Future Trends in China Mould Manufacturing
The future of china mould manufacture looks promising, with several trends shaping the industry:
1. Automation and Robotics
Increased automation through robotics is revolutionizing the manufacturing process, enhancing productivity and precision while reducing production costs. Manufacturers are rapidly adopting these technologies to remain competitive.
2. Environmentally Friendly Practices
With a global emphasis on sustainability, Chinese manufacturers are beginning to implement greener practices, such as reducing waste in the production process and using recyclable materials for molds.
3. Smart Manufacturing
The integration of the Internet of Things (IoT) into manufacturing allows for real-time monitoring of processes, enabling manufacturers to optimize production efficiency and respond to issues promptly.
4. Continuous Improvement and Innovation
Chinese manufacturers are committed to continuous improvement, investing in R&D to innovate new mould designs and production techniques that enhance performance and efficiency.
Choosing the Right Partner for Mould Manufacturing
When selecting a mould manufacturer, consider the following factors to ensure you choose the right partner:
- Experience and Reputation: Look for manufacturers with a strong industry reputation and proven experience in plastic mould making and injection moulding.
- Technology Capabilities: Evaluate the technology and machinery they utilize. Manufacturers who invest in state-of-the-art equipment are more likely to produce high-quality molds.
- Customer Support: Strong customer support and post-production services are essential for addressing potential issues and ensuring smooth operations.
- Portfolio and Case Studies: Reviewing case studies or a portfolio can visualize the manufacturer’s capabilities and quality of work.
Conclusion
In conclusion, the realm of china mould manufacture offers unmatched benefits for businesses looking for quality, efficiency, and innovation in plastic mold making and injection mould manufacturing. Companies like Hanking Mould exemplify the qualities needed for success in this competitive field, providing valuable resources to industries across the globe. As the sector continues to evolve, partnering with a knowledgeable and experienced manufacturer becomes increasingly crucial for companies striving to achieve excellence in their production processes.